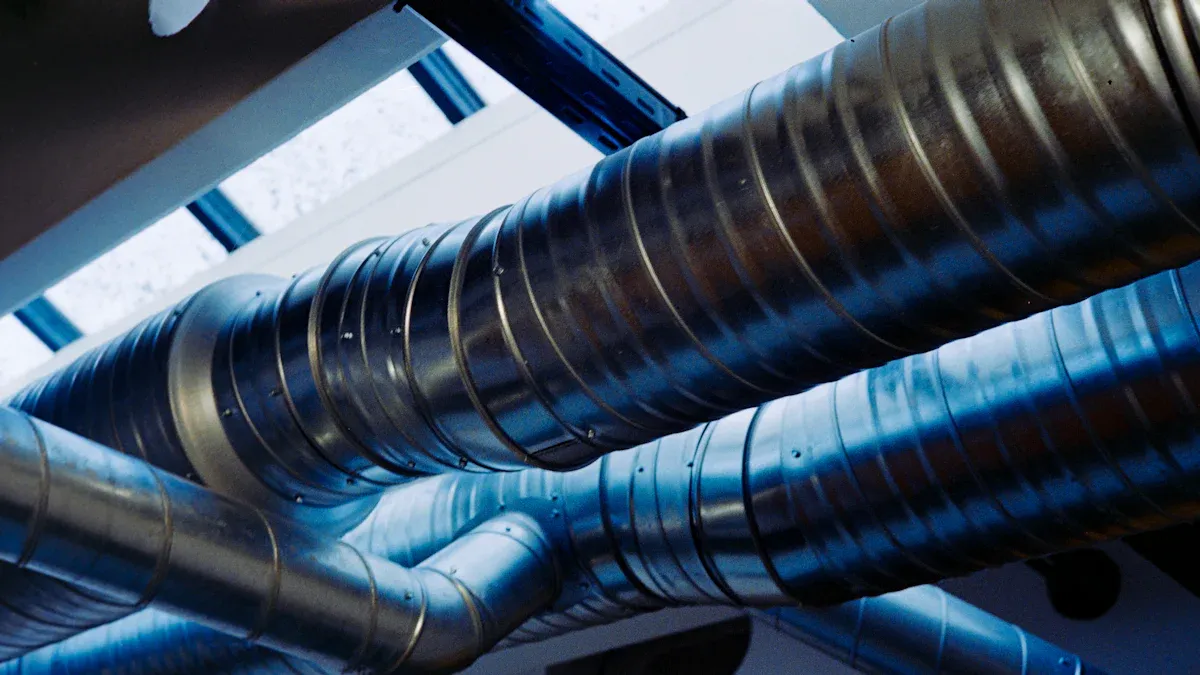
Safe and efficient hazardous location enclosure cooling requires three main elements. Understanding NEC classification is crucial. It’s also important to know the hazardous material groups involved. Selecting the right cooling system is essential as well. Technicians and facility managers must ensure that system certifications and features align with the specific hazards. This approach helps protect people, property, and processes from potential dangers.
Key Takeaways
- Learn about NEC classifications and material groups. This helps you pick the right cooling system for dangerous places. – Pick cooling systems that have the right certifications. Make sure they have features that fit the hazards. This keeps people and equipment safe. – Use closed-loop cooling and manage condensate well. This stops dust, water, and gases from getting inside enclosures. It also helps save energy. – Do regular maintenance and keep good records. This helps you avoid problems and makes cooling systems last longer and work better. – Ask experts for help to follow safety rules. Make clear procedures and make smart choices for cooling in hazardous places.
NEC Classifications

Image Source: cooltechx
Class I, Division 2
The National Electrical Code, or NEC, has a system to sort hazardous places. This system helps engineers and safety managers pick the right equipment for each spot. Class I, Division 2 areas have flammable gases or vapors, but only if something goes wrong. For example, a leak or a broken part can make these places dangerous. Most of the time, these areas are safe.
Class I, Division 2 places have fewer accidents than Class I, Division 1. Division 1 areas always have dangerous substances, so accidents happen more often. In oil and gas work, offshore drilling sites (Division 1) have more accidents than onshore sites (Division 2). Division 2 sites follow stricter safety rules and better ways of working, which makes them safer.
The NEC also uses zones and divisions to show how risky an area is. Zones tell how often dangerous stuff is there. Zone 0 means it is always there, but Zone 2 means it is there only sometimes. Divisions show if hazards are normal or only happen when something goes wrong. Equipment Protection Levels, or EPL, help match equipment to the risk, so people stay safe.
Classification | Description | Precautions |
---|---|---|
Class I | Places with flammable gases or vapors | Grounding, explosion-proof boxes, intrinsically safe equipment |
Class II | Places with combustible dust | Cleaning, dust collection, spark-proof tools |
Class III | Places with ignitable fibers or flyings | Maintenance, storage, flame-resistant clothes |
Material Groups
Material groups help people know what dangers are in a place. Engineers use real data from the USEPA ECOTOX and USACE ERED databases to learn about chemical risks. These databases give facts about how toxic chemicals are and how they affect the environment. If there is no data, models can guess the risks by looking at the chemical’s structure.
Hazard checks often put chemicals into groups by how risky they are, like how easily they catch fire or how poisonous they are. For example, studies on lithium-ion battery chemicals use both real data and models to check health and environmental dangers. This way, safety managers can understand where dangerous materials are and make good choices.
Machine learning models also use lists of hazardous materials to guess if dangerous stuff is in buildings. These models are very accurate and help with risk checks in demolition and environmental work. By using both real data and smart guesses, companies can find and handle dangers in tricky places.
Hazardous Location Enclosure Cooling
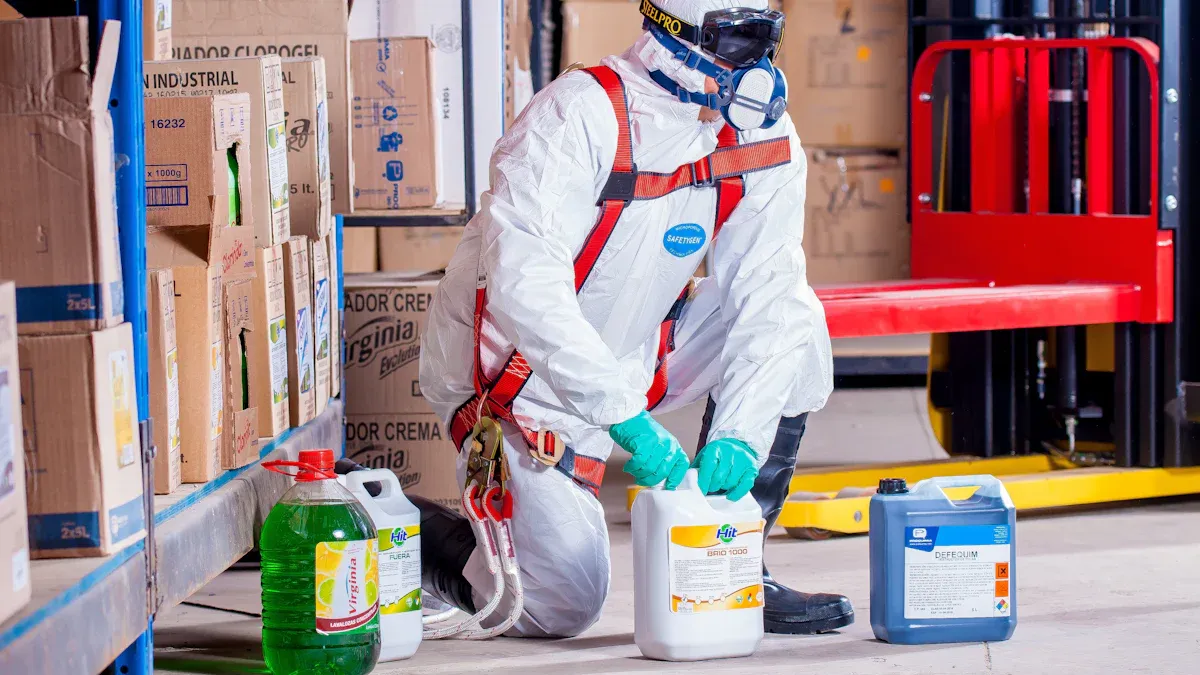
System Selection
Choosing the right system for hazardous location enclosure cooling keeps people and equipment safe. Every cooling system must fit the NEC classification and the material group in the area. For example, Group A is for acetylene. Group B is for hydrogen. Group C is for acetaldehyde. Group D is for gasoline and propane. Cooling systems need certifications for the exact group of flammable gas or vapor in the space. This helps stop fires and keeps things safe.
Key things to look for when picking a system are:
- The system must follow NEC hazardous location classifications: Class I, Division 2, Groups A, B, C, and D.
- It should have certifications like UL 60079-1 (flameproof), UL 60079-7 (increased safety), and UL 60079-31 (dust protection).
- Use enclosure materials such as stainless steel because it is strong and does not rust.
- Make sure the ingress protection ratings (IP67, IP68) keep out water and dust.
- Think about the environment, like temperature, humidity, and sunlight.
- Use things like sunshades, breathers, drains, heaters, and dehumidifiers to control inside conditions.
Tip: Always make sure the cooling system’s certification matches the hazardous material group in the area. This step lowers the chance of accidents and helps follow the rules.
Facility managers should also think about the size of the enclosure, how easy it is to reach, and if it needs regular care. All parts, like fittings and seals, must keep the right level of protection. Installing everything with certified fittings and the right tightness keeps the enclosure explosion-proof.
Compliance Risks
Using the wrong or non-compliant equipment in hazardous location enclosure cooling is very dangerous. Equipment that does not meet NEC or UL standards can start fires or explosions. It can also cause toxic leaks. Not following the rules can get companies in trouble and cause expensive delays.
Some common compliance risks are:
- Putting in cooling systems that are not certified for the hazardous material group.
- Using enclosures that do not keep out water or dust.
- Picking materials that rust or break down in tough places.
- Not keeping records of checks, repairs, or maintenance.
Note: Checking and fixing things often helps stop problems and keeps everyone safe. Writing down all work done is important for following the rules.
If things are tricky or special, it is smart to ask experts or manufacturers for help. They can explain NEC rules, help pick the right cooling system, and give good advice for hazardous location enclosure cooling. This makes things safer and helps the system last longer.
Key Features
Closed-Loop Systems
Closed-loop systems are very important for enclosure cooling. These systems keep inside air away from outside air. This stops dust, water, and flammable gases from getting in. Engineers use remote controls to make changes from outside. They do not need to open the enclosure or break the seal. This keeps the system safe and working well.
- Closed-loop systems block outside dirt and gases.
- Remote controls help change settings without opening the box.
- The system follows strict safety rules for hazardous places.
Metric / Feature | Description / Benefit |
---|---|
Real-time Pressure and Flow Monitoring | Gives steady data to help manage and control pressure. |
Use of Rotating Control Devices | Keeps the seal tight and makes a closed, pressurized system. |
Contained Return System | Makes work safer and more certain in risky areas. |
Condensate Management
Good condensate management systems make things safer and better. Instead of using drains that can clog, these systems dry up water inside the enclosure. This means less fixing and a dry space. Data shows using this water for cooling saves up to 35% energy. Exergy analysis shows a 31% drop in exergy use and a 5% rise in efficiency. These systems help keep the right temperature and support green building goals.
- Evaporative condensate management stops drain clogs.
- Saving energy and working better makes the system cheaper.
- Good condensate care helps the system last longer.
Tip: Good condensate management saves energy and helps the cooling system last longer.
Controls and Efficiency
Modern enclosure cooling uses smart controllers, sensors, and special screens. These tools let people watch and change settings right away. Operators can change cooling from far away. This means they do not need to open the enclosure and risk danger. Data from big buildings shows remote control and energy-saving features save lots of energy each year. These systems also cut down on carbon and other pollution.
- Smart controllers make things safer and work better.
- Remote access lets people change settings fast and safely.
- Energy-saving choices lower costs and help the planet.
Using smart controls and automation helps companies follow safety rules and work better.
Practical Tips
Expert Consultation
Facility managers and engineers sometimes have hard problems to solve. They work with hazardous location enclosure cooling. Talking to experts helps make sure systems are safe. Experts know all the rules and safety needs. They help projects follow standards from groups like AIA, ASHRAE, and AAMI. Many states use these standards for safe engineering.
Getting advice from experts helps teams make good SOPs. These clear SOPs help everyone do things the same way. This lowers mistakes and helps follow the rules. Training from experts keeps workers up to date. They learn about new rules and the best ways to work. Learning all the time helps everyone stay safe and follow the rules.
Industry stories show why expert help is good:
- Using the same steps cut data mistakes by 30% and made reports faster.
- Good SOPs helped pass inspections and get approvals.
- Using tech for documents saved time and lowered risks.
Benefit | Impact |
---|---|
Consistent SOPs | Fewer errors, better compliance |
Expert-led training | Improved staff awareness and safety culture |
Technology adoption | Streamlined audits and documentation |
Maintenance
Doing regular maintenance is very important for these cooling systems. Teams need to find the most important equipment. They use Failure Mode and Effects Analysis (FMEA) to pick what to fix first. Looking at maintenance data helps guess what might break next.
- Doing checks on time keeps equipment working longer.
- Regular checks help plan money and supplies.
- Keeping records helps teams get better and know when to fix or replace things.
Reliability-centered maintenance (RCM) uses data to focus on key jobs. Remote sensors can spot problems early. This means less downtime and more reliable work.
Writing down all maintenance and system checks helps teams fix problems fast and follow the rules.
Keeping up with care, using data, and asking experts keeps these cooling systems safe and working well.
Facility managers need to make sure the cooling system fits the dangers in each place. They must check that the system has the right certifications for the material group. This helps keep everyone safe and makes work go smoothly. Teams who focus on hazardous location enclosure cooling keep people and equipment safe. They should talk to experts and pick systems with smart features. This helps the system last longer and follow the rules.
For the best results, always check what the system needs and ask an expert before choosing.
FAQ
What does NEC Class I, Division 2 mean?
NEC Class I, Division 2 means there could be flammable gases or vapors if something breaks. Engineers use this label to pick safe equipment for these places.
Why is closed-loop cooling important in hazardous areas?
Closed-loop cooling stops outside air, dust, and gases from getting inside. This setup keeps important equipment safe and lowers the chance of fire or explosion.
How often should teams inspect hazardous location cooling systems?
Teams need to check these systems at least every three months. Regular checks help find problems early and keep everything safe and working well.
What certifications should enclosure cooling systems have?
Cooling systems need certifications like UL 60079-1, UL 60079-7, and UL 60079-31. These show the system is safe for hazardous places.
Who should facility managers contact for complex cooling needs?
Facility managers should talk to certified experts or manufacturers. These people know NEC rules and can suggest the best answers for special hazards.